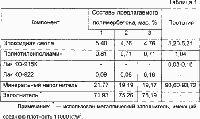
СН 525-80
СТРОИТЕЛЬНЫЕ НОРМЫ
Инструкция
по технологии приготовления полимербетонов и
изделий из них
Дата введения 1981-01-01
РАЗРАБОТАНЫ НИИЖБ Госстроя СССР с участием институтов Гипроцветмет Минцвета СССР, МИИТ Главного управления учебных заведений МПС СССР, МИТХТ Министерства высшего и среднего образования РСФСР.
ВНЕСЕНЫ НИИЖБом Госстроя СССР
УТВЕРЖДЕНЫ постановлением государственного комитета СССР по делам строительства от 19 мая 1980 г. N 69
1. ОСНОВНЫЕ ПОЛОЖЕНИЯ
1.1. Требования настоящей Инструкции должны применяться при проектировании составов, приготовлении и контроле качества полимербетонов на фурфурол-ацетоновых ФАМ (ФА), полиэфирных ПН, карбамидоформальдегидных КФ-Ж, фурано-эпоксидных ФАЭД смолах и мономере метилметакрилате ММА, предназначенных для изготовления изделий, эксплуатирующихся при систематическом воздействии сильноагрессивных сред и температур не выше плюс 80 град.С и не ниже минус 40 град.С.
1.2. Полимербетоны относятся к специальным видам бетонов и подразделяются по следующим признакам:
основному назначению;
виду вяжущего;
виду заполнителей.
1.3. Наименования полимербетонов определенных видов должны включать все признаки, установленные настоящей Инструкцией (например, полимербетон ПН конструкционный на плотных заполнителях).
Для армированных материалов перед названием указывается вид армирующего материала (например, сталеполимербетон ФАМ конструкционный на пористых заполнителях).
1.4. Для полимербетонов, характеризуемых наиболее часто применяемыми сочетаниями признаков, устанавливаются следующие наименования: «полимербетон тяжелый», «полимербетон легкий».
2. МАТЕРИАЛЫ ДЛЯ ПРИГОТОВЛЕНИЯ ПОЛИМЕРБЕТОНОВ
Смолы, отвердители и пластификаторы
2.1. Для приготовления полимербетонов следует применять следующие синтетические смолы:
фурфурол-ацетоновая смола ФАМ или ФА (ТУ 6-05-1618-73);
ненасыщенная полиэфирная смола ПН-1 (МРТУ 6-05-1082-76) или ПН-63 (ОСТ 6-05-431-78);
карбамидоформальдегидная КФ-Ж (ГОСТ 14231-78);
фурано-эпоксидная смола ФАЭД-20 (ТУ-59-02-039.13-78);
эфир метиловый метакриловой кислоты (мономер метилметакрилат) ММА (ГОСТ 16505-70).
2.2. В качестве отвердителей синтетических смол используются:
для фурфурол-ацетоновых смол ФАМ и ФА — бензолсульфокислота БСК (ТУ 6.1425-74);
для полиэфирных смол ПН-1 и ПН-63 — гидроперекись изопропилбензола ГП (ТУ 38-10293-75);
для карбамидоформальдегидной КФ-Ж — солянокислый анилин СКА (ГОСТ 5822-78);
для фурано-эпоскидной смолы ФАЭД-20 — полиэтиленполиамин ПЭПА (ТУ 6-02-594-70);
для метилметакрилата ММА — система, состоящая из технического диметиланилина ДМА (ГОСТ 2168-71) и перекиси бензоила ПБ (ГОСТ 14888-78).
2.3. В качестве ускорителя твердения полиэфирных смол используется нафтенат кобальта НК (МРТУ 6-05-1075-76).
2.4. Для снижения летучести метилметакрилата следует применять нефтяной парафин (ГОСТ 16960-71*).
2.5. Для стабилизации протекания реакция отверждения метилметакрилата следует применять эмульсионный полистирол (ГОСТ 20282-74*).
2.6. В качестве пластифицирующих добавок следует применять:
катапин (ТУ 6-01-1026-75);
алкамон ОС-2 (ГОСТ 10106-75);
меламино-формальдегидную смолу К-421-02 (ТУ 6-10-1022-78);
сульфированные нафталинформальдегидные соединения пластификатор С-3 (ТУ 6-14-10-205-78).
2.7. Хранение материалов, перечисленных в пп.2.1-2.6 настоящей Инструкции, производится в соответствии с требованиями ГОСТ и ТУ. Перед применением необходимо провести проверку соответствия продуктов требованиям ГОСТ и ТУ.
Требования к заполнителям
2.8. В качестве крупного заполнителя для тяжелых полимербетонов может применяться щебень из естественного камня или щебень из гравия. Щебень и щебень, дробленный из гравия, должны отвечать требованиям ГОСТ 8267-75, ГОСТ 8268-74*, ГОСТ 10260-74* и требованиям настоящей Инструкции.
Применение щебня из осадочных горных пород не допускается.
В качестве крупных пористых заполнителей для полимербетонов следует применять керамзитовый гравий, шунгизитовый гравий и аглопоритовый щебень, соответствующие требованиям ГОСТ 9759-76, ГОСТ 19345-73, ГОСТ 11991-76 и требованиям настоящей Инструкции.
2.9. Для приготовления тяжелых полимербетонов высокий плотности следует применять щебень следующих фракций:
при наибольшем диаметре, равном 20 мм, следует применять щебень одной фракции 10-20 мм;
при наибольшем диаметре, равном 40 мм, следует применять щебень двух фракций 10-20 и 20-40 мм.
Зерновой состав каждой фракции должен отвечать требованиям ГОСТ 10268-70*. При этом наибольший диаметр выбирается в пределах 0,2 минимального сечения конструкции.
2.10. Для приготовления полимербетонов на пористых заполнителях должен применяться крупный пористый заполнитель с максимальной крупностью 20 мм.
Крупный пористый заполнитель следует делить по размеру на две фракции 5-10 и 10-20 мм. Зерновой состав каждой фракции должен отвечать требованиям ГОСТ 9759-76.
Соотношение между фракциями 5-10 и 10-20 мм в смеси следует принимать 40:60 (в процентах по массе).
2.11. Для приготовления полимербетонов в качестве мелкого заполнителя следует применять кварцевые пески, отвечающие требованиям ГОСТ 8736-77 и настоящей Инструкции:
природные (в естественном состоянии), природные фракционированные и природные обогащенные;
дробленые и дробленые фракционированные.
Зерновой состав мелкого заполнителя в полимербетоне должен соответствовать кривой просеивания, приведенной в ГОСТ 10268-70*. Модуль крупности песка должен быть в пределах от 2 до 3.
2.12. Содержание в природных и дробленых песках зерен, проходящих через сито N 014, не должно превышать 2%, а пылевидных, илистых и глинистых частиц, определяемых отмучиванием, не должно превышать 0,5%.
2.13. Испытание тяжелых крупных заполнителей следует производить по ГОСТ 9758-77, а песка — по ГОСТ 8735-75.
2.14. Крупные и мелкие заполнители должны быть сухими влажность не более 0,5%.
2.15. Не допускается загрязнение заполнителей карбонатами (мел, мрамор, известняк), основаниями (известь, цемент) и металлической пылью (стальной, цинковой).
Требования к наполнителям
2.16. Для приготовления полимербетонов в качестве наполнителя следует применять андезитовую муку (ТУ-6-12-101-77), кварцевую муку (ГОСТ 9077-59), маршалит (ГОСТ 8736-77), диабазовую муку, графитовый порошок (ГОСТ 8295-73).
2.17. В качестве наполнителей допускается применение молотых тяжелого и аглопоритового щебня и кварцевого песка.
2.18. Удельная поверхность наполнителей, перечисленных в пп. 2.16, 2.17 настоящей Инструкции, определенная по ГОСТ 310.2-76, должна быть в пределах от 2500 до 3000 кв.см/г.
2.19. В качестве водосвязующей добавки при приготовлении полимербетонов КФ-Ж используется полуводный строительный гипс (ГОСТ 125-70).
2.20. Влажность наполнителей, перечисленных в пп. 2.16, 2.17 и 2.19 настоящей Инструкции, не более 1%.
2.21. Кислотостойкость песка и наполнителей, определяемая по ГОСТ 473.1-72, должна быть не ниже 97-98%.
3. Составы полимербетонов
3.1. Составы полимербетонов следует принимать согласно табл.1-3 настоящей Инструкции.
3.2. В качестве пластификаторов для составов на фурфурол-ацетоновых смолах ФАМ (ФА) и полиэфирных смолах ПН-1 и ПН-63 следует применять катапин или алкамон ОС-2 в количестве 0,5-1% от массы смолы.
3.3. В качестве пластификатора для составов на метилметакрилате ММА следует применять меламино-формальдегидную смолу К-421-02 в количестве 0,5-1% от массы мономера.
3.4. В качестве пластификатора для составов на смоле КФ-Ж следует применять пластификатор С-3, который вводится в пересчете на сухое вещество в количестве 0,5-1% от массы смолы КФ-Ж.
4. Приготовление полимербетонов
4.1. Приготовление полимербетонной смеси должно включать следующие операции:
промыв заполнителей;
сушка наполнителей и заполнителей;
фракционирование заполнителей;
подготовка отвердителей и ускорителей;
дозирование составляющих;
перемешивание составляющих.
4.2. Промыв производится только в том случае, если заполнители не отвечают требованиям разд.2 настоящей Инструкции.
4.3. Наполнители и заполнители должны подвергаться сушке для обеспечения влажности материалов не выше указанной в пп.2.14 и 2.20 настоящей Инструкции.
4.4. Сушку материалов следует производить в сушильных барабанах или других аппаратах (печах, термошкафах).
4.5. При необходимости после сушки заполнители подаются на сита для рассева по фракциям, а затем заполнители и наполнители загружаются в соответствующие бункера-накопители.
4.6. Температура наполнителей и заполнителей перед подачей в дозаторы должна быть в пределах 20+5 град.С.
4.7. Смолы, отвердители, ускоритель и пластификаторы, перечисленные в разд.2 настоящей Инструкции, за исключением бензолсульфокислоты (БСК) и солянокислого анилина (СКА), должны перекачиваться со склада в соответствующие емкости-накопители центробежными насосами типа ВК и АСЦЛ.
4.8. Бензолсульфокислота перед загрузкой в емкость-накопитель должна предварительно расплавляться при температуре 65+/-5 град.С в емкости, снабженной водяной рубашкой и обогреваемой паровыми регистрами. Расходная емкость для БСК должна быть снабжена подогревом для поддерживания температуры расплавленной БСК в пределах от 40 до 45 град.С.
4.9. Емкость для расплава, емкости-накопители, насосы, трубопроводы и расходная емкость для БСК должны выполняться из кислотостойкой стали.
4.10. Дозирование составляющих полимербетонной смеси следует производить по массе дозаторами, обеспечивающими следующую точность дозирования;
смолы, наполнителя, отвердителя — +/- 1% по массе;
заполнителей (песка и щебня) — +/- 2% по массе.
Дозировочные устройства должны отвечать требованиям ГОСТ 13712-68**.
Дозирование жидких составляющих полимербетонной смеси допускается производить насосами-дозаторами типа НД-400/16 или НД-1000/16.
4.11. Перемешивание составляющих полимербетонных смесей ФАМ (ФА), ПН, КФ-Ж и ФАЭД должно включать две стадии:
приготовление мастики;
приготовление полимербетонной смеси.
Таблица 1
+————————————————————————————————+
¦ ¦ ¦ ¦ Состав 1 ¦ Состав 2 ¦ Состав 3 ¦ Состав 4 ¦
¦ ¦ ¦ +—————-+—————-+—————-+—————-¦
¦ ¦ ¦ ¦Тяжелый полимер-¦Полимербетон ФАМ¦Тяжелый полимер-¦Полимербетон ¦
¦ N ¦ ¦ Размер ¦ бетон ФАМ (ФА) ¦(ФА) на пористых¦ бетон ФАЭД ¦ФАЭД на пористых¦
¦п.п.¦ Составляющие ¦фракций,¦ ¦ заполнителях ¦ ¦ заполнителях ¦
¦ ¦ ¦ мм +—————-+—————-+—————-+—————-¦
¦ ¦ ¦ ¦расход ¦расход ¦расход ¦расход ¦расход ¦расход ¦расход ¦расход ¦
¦ ¦ ¦ ¦состав-¦состав- ¦состав-¦состав- ¦состав-¦состав- ¦состав-¦состав- ¦
¦ ¦ ¦ ¦ляющих,¦ляющих, ¦ляющих,¦ляющих, ¦ляющих,¦ляющих, ¦ляющих,¦ляющих, ¦
¦ ¦ ¦ ¦в про- ¦кг/куб.м¦в про- ¦кг/куб.м¦в про- ¦кг/куб.м¦в про- ¦кг/куб.м¦
¦ ¦ ¦ ¦центах ¦ ¦центах ¦ ¦центах ¦ ¦центах ¦ ¦
¦ ¦ ¦ ¦по мас-¦ ¦по мас-¦ ¦по мас-¦ ¦по мас-¦ ¦
¦ ¦ ¦ ¦се ¦ ¦се ¦ ¦се ¦ ¦се ¦ ¦
+—-+—————+———+——-+———+——-+———+——-+———+——-+———¦
¦ 1 ¦Гранитный ще- ¦ 20-40 ¦ 50-51 ¦1200- ¦ — ¦ — ¦ 49-50 ¦ 1180- ¦ — ¦ — ¦
¦ ¦бень ¦ ¦ ¦ 1220 ¦ ¦ ¦ ¦ 1200 ¦ ¦ ¦
¦ ¦ ¦ ¦ ¦ ¦ ¦ ¦ ¦ ¦ ¦ ¦
¦ 2 ¦Гранитный ще- ¦ 10-20 ¦ 3-3,5 ¦ 72-84 ¦ — ¦ — ¦ 1-2 ¦ 24-48 ¦ — ¦ — ¦
¦ ¦бень ¦ ¦ ¦ ¦ ¦ ¦ ¦ ¦ ¦ ¦
¦ ¦ ¦ ¦ ¦ ¦ ¦ ¦ ¦ ¦ ¦ ¦
¦ 3 ¦Пористый ще- ¦ 10-20 ¦ — ¦ — ¦ 21-22 ¦380-400 ¦ — ¦ — ¦ 20-21 ¦360-380 ¦
¦ ¦бень или гра- ¦ ¦ ¦ ¦ ¦ ¦ ¦ ¦ ¦ ¦
¦ ¦вий ¦ ¦ ¦ ¦ ¦ ¦ ¦ ¦ ¦ ¦
¦ ¦ ¦ ¦ ¦ ¦ ¦ ¦ ¦ ¦ ¦ ¦
¦ 4 ¦Пористый ще- ¦ 5-10 ¦ — ¦ — ¦ 15-16 ¦270-290 ¦ — ¦ — ¦ 14-15 ¦250-270 ¦
¦ ¦бень или гра- ¦ ¦ ¦ ¦ ¦ ¦ ¦ ¦ ¦ ¦
¦ ¦вий ¦ ¦ ¦ ¦ ¦ ¦ ¦ ¦ ¦ ¦
¦ ¦ ¦ ¦ ¦ ¦ ¦ ¦ ¦ ¦ ¦ ¦
¦ 5 ¦Песок кварце- ¦ 0,15-5 ¦ 23 ¦ 550 ¦ 31 ¦ 560 ¦ 18-19 ¦430-460 ¦ 30-31 ¦540-560 ¦
¦ ¦вый ¦ ¦ ¦ ¦ ¦ ¦ ¦ ¦ ¦ ¦
¦ ¦ ¦ ¦ ¦ ¦ ¦ ¦ ¦ ¦ ¦ ¦
¦ 6 ¦Наполнитель ¦Менее ¦12-12,5¦288-300 ¦ 18,5 ¦ 335 ¦15,5- ¦370-400 ¦ 18-19 ¦325-340 ¦
¦ ¦ ¦ 0,15 ¦ ¦ ¦ ¦ ¦ 16,5 ¦ ¦ ¦ ¦
¦ ¦ ¦ ¦ ¦ ¦ ¦ ¦ ¦ ¦ ¦ ¦
¦ 7 ¦Фурфурол-аце- ¦ — ¦ 8-8,5 ¦190-205 ¦11,5-12¦208-215 ¦ — ¦ — ¦ — ¦ — ¦
¦ ¦тоновая смола ¦ ¦ ¦ ¦ ¦ ¦ ¦ ¦ ¦ ¦
¦ ¦ФАМ (ФА) ¦ ¦ ¦ ¦ ¦ ¦ ¦ ¦ ¦ ¦
¦ ¦ ¦ ¦ ¦ ¦ ¦ ¦ ¦ ¦ ¦ ¦
¦ 8 ¦Бензолсульфо- ¦ — ¦1,5-1,7¦ 36-41 ¦2,3-2,4¦ 41-43 ¦ — ¦ — ¦ — ¦ — ¦
¦ ¦кислота БСК ¦ ¦ ¦ ¦ ¦ ¦ ¦ ¦ ¦ ¦
¦ ¦ ¦ ¦ ¦ ¦ ¦ ¦ ¦ ¦ ¦ ¦
¦ 9 ¦Фурано-эпок- ¦ — ¦ — ¦ — ¦ — ¦ — ¦11,5-12¦275-290 ¦ 13-14 ¦235-250 ¦
¦ ¦сидная смола ¦ ¦ ¦ ¦ ¦ ¦ ¦ ¦ ¦ ¦
¦ ¦ФАЭД-20 ¦ ¦ ¦ ¦ ¦ ¦ ¦ ¦ ¦ ¦
¦ ¦ ¦ ¦ ¦ ¦ ¦ ¦ ¦ ¦ ¦ ¦
¦ 10 ¦Полиэтиленпо- ¦ — ¦ — ¦ — ¦ — ¦ — ¦2,2-2,4¦ 53-58 ¦2,5-2,7¦ 45-49 ¦
¦ ¦лиамин (ПЭПА) ¦ ¦ ¦ ¦ ¦ ¦ ¦ ¦ ¦ ¦
¦ ¦ ¦ ¦ ¦ ¦ ¦ ¦ ¦ ¦ ¦ ¦
¦ 11 ¦Пластификатор ¦ — ¦0,5-1% ¦ 1-2 ¦0,5-1% ¦ 1-2 ¦ — ¦ — ¦ — ¦ — ¦
¦ ¦ ¦ ¦от мас-¦ ¦от мас-¦ ¦ ¦ ¦ ¦ ¦
¦ ¦ ¦ ¦сы смо-¦ ¦сы смо-¦ ¦ ¦ ¦ ¦ ¦
¦ ¦ ¦ ¦лы ¦ ¦лы ¦ ¦ ¦ ¦ ¦ ¦
Таблица 2
+————————————————————————————————+
¦ ¦ ¦ ¦ Состав 5 ¦ Состав 6 ¦ Состав 7 ¦ Состав 8 ¦
¦ ¦ ¦ +—————-+—————-+—————-+—————-¦
¦ ¦ ¦ ¦Тяжелый полимер-¦Полимербетон ПН ¦Тяжелый полимер-¦Полимербетон ¦
¦ N ¦ ¦ Размер ¦ бетон ПН ¦ на пористых¦ бетон КФ-Ж ¦КФ-Ж на пористых¦
¦п.п.¦ Составляющие ¦фракций,¦ ¦ заполнителях ¦ ¦ заполнителях ¦
¦ ¦ ¦ мм +—————-+—————-+—————-+—————-¦
¦ ¦ ¦ ¦расход ¦расход ¦расход ¦расход ¦расход ¦расход ¦расход ¦расход ¦
¦ ¦ ¦ ¦состав-¦состав- ¦состав-¦состав- ¦состав-¦состав- ¦состав-¦состав- ¦
¦ ¦ ¦ ¦ляющих,¦ляющих, ¦ляющих,¦ляющих, ¦ляющих,¦ляющих, ¦ляющих,¦ляющих, ¦
¦ ¦ ¦ ¦в про- ¦кг/куб.м¦в про- ¦кг/куб.м¦в про- ¦кг/куб.м¦в про- ¦кг/куб.м¦
¦ ¦ ¦ ¦центах ¦ ¦центах ¦ ¦центах ¦ ¦центах ¦ ¦
¦ ¦ ¦ ¦по мас-¦ ¦по мас-¦ ¦по мас-¦ ¦по мас-¦ ¦
¦ ¦ ¦ ¦се ¦ ¦се ¦ ¦се ¦ ¦се ¦ ¦
+—-+—————+———+——-+———+——-+———+——-+———+——-+———¦
¦ 1 ¦Гранитный ще- ¦ 20-40 ¦ 50-52 ¦1200- ¦ — ¦ — ¦ 49-50 ¦ 1170- ¦ — ¦ — ¦
¦ ¦бень ¦ ¦ ¦ 1250 ¦ ¦ ¦ ¦ 1200 ¦ ¦ ¦
¦ ¦ ¦ ¦ ¦ ¦ ¦ ¦ ¦ ¦ ¦ ¦
¦ 2 ¦Гранитный ще- ¦ 10-20 ¦ 4-4,5 ¦ 96-108 ¦ — ¦ — ¦ 3-3,5 ¦ 72-84 ¦ — ¦ — ¦
¦ ¦бень ¦ ¦ ¦ ¦ ¦ ¦ ¦ ¦ ¦ ¦
¦ ¦ ¦ ¦ ¦ ¦ ¦ ¦ ¦ ¦ ¦ ¦
¦ 3 ¦Пористый ще- ¦ 10-20 ¦ — ¦ — ¦ 22-23 ¦400-415 ¦ — ¦ — ¦ 22-23 ¦400-415 ¦
¦ ¦бень или гра- ¦ ¦ ¦ ¦ ¦ ¦ ¦ ¦ ¦ ¦
¦ ¦вий ¦ ¦ ¦ ¦ ¦ ¦ ¦ ¦ ¦ ¦
¦ ¦ ¦ ¦ ¦ ¦ ¦ ¦ ¦ ¦ ¦ ¦
¦ 4 ¦Пористый ще- ¦ 5-10 ¦ — ¦ — ¦ 15-16 ¦270-290 ¦ — ¦ — ¦ 15-16 ¦270-290 ¦
¦ ¦бень или гра- ¦ ¦ ¦ ¦ ¦ ¦ ¦ ¦ ¦ ¦
¦ ¦вий ¦ ¦ ¦ ¦ ¦ ¦ ¦ ¦ ¦ ¦
¦ ¦ ¦ ¦ ¦ ¦ ¦ ¦ ¦ ¦ ¦ ¦
¦ 5 ¦Песок кварце- ¦ 0,15-5 ¦ 22-24 ¦ 530-570¦ 30-31 ¦540-560 ¦ 22-23 ¦530-560 ¦ 27-28 ¦485-505 ¦
¦ ¦вый ¦ ¦ ¦ ¦ ¦ ¦ ¦ ¦ ¦ ¦
¦ ¦ ¦ ¦ ¦ ¦ ¦ ¦ ¦ ¦ ¦ ¦
¦ 6 ¦Наполнитель ¦Менее ¦11-12 ¦264-288 ¦ 18-19 ¦325-340 ¦ 10-11 ¦240-265 ¦ 17-18 ¦305-325 ¦
¦ ¦ ¦ 0,15 ¦ ¦ ¦ ¦ ¦ ¦ ¦ ¦ ¦
¦ ¦ ¦ ¦ ¦ ¦ ¦ ¦ ¦ ¦ ¦ ¦
¦ 7 ¦Полиэфирная ¦ — ¦ 8-8,5 ¦192-204 ¦11-12 ¦200-217 ¦ — ¦ — ¦ — ¦ — ¦
¦ ¦смола ПН-1 или¦ ¦ ¦ ¦ ¦ ¦ ¦ ¦ ¦ ¦
¦ ¦ПН-68 ¦ ¦ ¦ ¦ ¦ ¦ ¦ ¦ ¦ ¦
¦ ¦ ¦ ¦ ¦ ¦ ¦ ¦ ¦ ¦ ¦ ¦
¦ 8 ¦Гидроперекись ¦ — ¦0,33- ¦8-8,5 ¦0,45- ¦ 8-9 ¦ — ¦ — ¦ — ¦ — ¦
¦ ¦изопропилбен- ¦ ¦ 0,35 ¦ ¦ 0,5 ¦ ¦ ¦ ¦ ¦ ¦
¦ ¦зола ¦ ¦ ¦ ¦ ¦ ¦ ¦ ¦ ¦ ¦
¦ ¦ ¦ ¦ ¦ ¦ ¦ ¦ ¦ ¦ ¦ ¦
¦ 9 ¦Нафтенат ко- ¦ — ¦0,66- ¦ 16-18 ¦0,9-1 ¦ 16-18 ¦ — ¦ — ¦ — ¦ — ¦
¦ ¦бальта НК ¦ ¦ 0,7 ¦ ¦ ¦ ¦ ¦ ¦ ¦ ¦
¦ ¦ ¦ ¦ ¦ ¦ ¦ ¦ ¦ ¦ ¦ ¦
¦ 10 ¦Карбамидофор- ¦ — ¦ — ¦ — ¦ — ¦ — ¦ 8,5-9 ¦205-216 ¦11,5- ¦205-225 ¦
¦ ¦мальдегидная ¦ ¦ ¦ ¦ ¦ ¦ ¦ ¦ 12,5 ¦ ¦
¦ ¦смола КФ-Ж ¦ ¦ ¦ ¦ ¦ ¦ ¦ ¦ ¦ ¦
¦ ¦ ¦ ¦ ¦ ¦ ¦ ¦ ¦ ¦ ¦ ¦
¦ 11 ¦Фосфогипс или ¦ Менее ¦ — ¦ — ¦ — ¦ — ¦ 4-5 ¦ 86-120 ¦ 5-6 ¦ 90-110 ¦
¦ ¦гипс ¦ 0,15 ¦ ¦ ¦ ¦ ¦ ¦ ¦ ¦ ¦
¦ ¦ ¦ ¦ ¦ ¦ ¦ ¦ ¦ ¦ ¦ ¦
¦ 12 ¦Солянокислый ¦ — ¦ — ¦ — ¦ — ¦ — ¦ 3-4% ¦6,5-8,5 ¦ 3-4% ¦6,5-8,5 ¦
¦ ¦анилин СКА ¦ ¦ ¦ ¦ ¦ ¦от мас-¦ ¦от мас-¦ ¦
¦ ¦ ¦ ¦ ¦ ¦ ¦ ¦сы УКС ¦ ¦сы УКС ¦ ¦
¦ ¦ ¦ ¦ ¦ ¦ ¦ ¦ ¦ ¦ ¦ ¦
¦ 13 ¦Пластификатор ¦ — ¦0,5-1% ¦ 1-2 ¦0,5-1% ¦ 1-2 ¦ — ¦ — ¦ — ¦ — ¦
¦ ¦ ¦ ¦от мас-¦ ¦от мас-¦ ¦ ¦ ¦ ¦ ¦
¦ ¦ ¦ ¦сы смо-¦ ¦сы смо-¦ ¦ ¦ ¦ ¦ ¦
¦ ¦ ¦ ¦лы ¦ ¦лы ¦ ¦ ¦ ¦ ¦ ¦
Таблица 3
+——————————————————————+
¦ ¦ ¦ ¦ Состав 9 ¦ Состав 10 ¦
¦ ¦ ¦ +—————-+—————-¦
¦ ¦ ¦ ¦Тяжелый полимер-¦Полимербетон ¦
¦ N ¦ ¦ Размер ¦ бетон ММА ¦ММА на пористых¦
¦п.п.¦ Составляющие ¦фракций,¦ ¦ заполнителях ¦
¦ ¦ ¦ мм +—————-+—————-¦
¦ ¦ ¦ ¦расход ¦расход ¦расход ¦расход ¦
¦ ¦ ¦ ¦состав-¦состав- ¦состав-¦состав- ¦
¦ ¦ ¦ ¦ляющих,¦ляющих, ¦ляющих,¦ляющих, ¦
¦ ¦ ¦ ¦в про- ¦кг/куб.м¦в про- ¦кг/куб.м¦
¦ ¦ ¦ ¦центах ¦ ¦центах ¦ ¦
¦ ¦ ¦ ¦по мас-¦ ¦по мас-¦ ¦
¦ ¦ ¦ ¦се ¦ ¦се ¦ ¦
+—-+——————+———+——-+———+——-+———¦
¦ 1 ¦Гранитный щебень ¦ 20-40 ¦ 46-47 ¦1100- ¦ — ¦ — ¦
¦ ¦ ¦ ¦ ¦ 1130 ¦ ¦ ¦
¦ ¦ ¦ ¦ ¦ ¦ ¦ ¦
¦ 2 ¦Гранитный щебень ¦ 10-20 ¦ 3-4 ¦ 70-95 ¦ — ¦ — ¦
¦ ¦ ¦ ¦ ¦ ¦ ¦ ¦
¦ ¦ ¦ ¦ ¦ ¦ ¦ ¦
¦ 3 ¦Пористый щебень ¦ 10-20 ¦ — ¦ — ¦ 22-23 ¦390-415 ¦
¦ ¦ ¦ ¦ ¦ ¦ ¦ ¦
¦ 4 ¦Пористый щебень ¦ 5-10 ¦ — ¦ — ¦ 15-16 ¦270-290 ¦
¦ ¦или гравий ¦ ¦ ¦ ¦ ¦ ¦
¦ ¦ ¦ ¦ ¦ ¦ ¦ ¦
¦ 5 ¦Песок кварцевый ¦ 0,15-5 ¦ 30-32 ¦ 720-770¦ 32-34 ¦575-610 ¦
¦ ¦ ¦ ¦ ¦ ¦ ¦ ¦
¦ 6 ¦Наполнитель ¦Менее ¦ 8-9 ¦190-215 ¦ 16-18 ¦290-320 ¦
¦ ¦ ¦ 0,15 ¦ ¦ ¦ ¦ ¦
¦ ¦ ¦ ¦ ¦ ¦ ¦ ¦
¦ 7 ¦Метилметакрилат ¦ — ¦ 8-8,5 ¦190-205 ¦10,5- ¦190-205 ¦
¦ ¦ ¦ ¦ ¦ ¦ 11,5 ¦ ¦
¦ ¦ ¦ ¦ ¦ ¦ ¦ ¦
¦ 8 ¦Парафин нефтяной ¦ — ¦0,5% от¦ 1-1,1 ¦0,5% от¦ 0,9-1 ¦
¦ ¦ ¦ ¦массы ¦ ¦массы ¦ ¦
¦ ¦ ¦ ¦ММА ¦ ¦смолы ¦ ¦
¦ ¦ ¦ ¦ ¦ ¦ ¦ ¦
¦ 9 ¦Эмульсионный поли-¦ — ¦0,4-0,5¦ 10-12 ¦0,5- ¦ 9-10 ¦
¦ ¦стирол ¦ ¦ ¦ ¦ 0,55¦ ¦
¦ ¦ ¦ ¦ ¦ ¦ ¦ ¦
¦ 10 ¦Диметиланилин ¦ — ¦0,2- ¦ 5-6 ¦0,2-0,3¦3,5-5,5 ¦
¦ ¦ ¦ ¦ 0,25¦ ¦ ¦ ¦
¦ ¦ ¦ ¦ ¦ ¦ ¦ ¦
¦ 11 ¦Паста из перекиси ¦ — ¦0,6-0,7¦ 14-17 ¦0,6-0,8¦ 11-14,5¦
¦ ¦бензоила и дибу- ¦ ¦ ¦ ¦ ¦ ¦
¦ ¦тилфталата ¦ ¦ ¦ ¦ ¦ ¦
¦ ¦ ¦ ¦ ¦ ¦ ¦ ¦
¦ 12 ¦Пластификатор ¦ — ¦0,5-1% ¦ 1-2 ¦0,5-1% ¦ 1-2 ¦
¦ ¦ ¦ ¦от мас-¦ ¦от мас-¦ ¦
¦ ¦ ¦ ¦сы мо- ¦ ¦сы мо- ¦ ¦
¦ ¦ ¦ ¦номера ¦ ¦номера ¦ ¦
4.12. Перемешивание составляющих полимербетонной смеси ФАМ (ФА).
а. Приготовление мастики должно проводиться в следующем порядке:
подача в высокоскоростной смеситель отдозированного количества смолы ФАМ (ФА) и пластификатора и перемешивание их в течение 10 с, скорость вращения рабочего органа смесителя 600-800 об/мин;
подача в работающий смеситель отдозированного количества наполнителя и перемешивание смеси в течение 30-60 с;
подача в работающий смеситель отдозированного количества отвердителя БСК и перемешивание смеси в течение 30 с;
выгрузка мастики из работающего смесителя в бетоносмеситель в течение 25-30 с.
Общее время приготовления мастики должно быть не более 100 с, а с учетом выгрузки — не более 2 мин.
б. Приготовление полимербетонной смеси ФАМ (ФА) должно производиться в следующем порядке:
загрузка заполнителей и перемешивание их в бетоносмесителе в течение 1-2 мин;
подача в бетоносмеситель мастики, приготовленной на первой стадии смешения, в течение 15-30 с;
перемешивание полимербетонной смеси в бетоносмесителе в течение 2-3 мин;
выгрузка полимербетонной смеси из смесителя в течение 20-30 с.
4.13. Перемешивание составляющих полимербетонной смеси ПН.
а. Приготовление мастики следует проводить в следующем порядке:
необходимое для одного замеса количество смолы делится на две равные части, подается в два работающих скоростных смесителя, скорость вращения рабочего органа смесителя 600-800 об/мин;
подача в первый смеситель отдозированного количества отвердителя ГП и пластификатора, а во второй — ускорителя НК и перемешивание смесей в течение 30 с;
одновременная подача в третий работающий смеситель отдозированного количества наполнителя и содержимого первого и второго смесителей и перемешивание смеси в течение 30-60 с;
выгрузка мастики из работающего смесителя в бетоносмеситель в течение 10-15 с.
Общее время приготовления мастики должно быть не более 1,5 мин., а с учетом выгрузки — не более 2 мин.
б. Технологические операции по приготовлению полимербетонной смеси ПН должны выполняться в соответствии с требованиями п.4.12б настоящей Инструкции.
4.14. Перемешивание составляющих полимербетонной смеси КФ-Ж.
а. Приготовление мастики должно проводиться в следующем порядке:
подача в высокоскоростной смеситель отдозированного количества смолы КФ-Ж и пластификатора С-3 и перемешивание в течение 10 с, скорость вращения рабочего органа смесителя 600-800 об/мин;
подача в рабочий смеситель отдозированного количества наполнителя и гипса и перемешивание смеси в течение 30-60 с;
подача в работающий смеситель отдозированного количества отвердителя СКА и перемешивание смеси в течение 30 с;
выгрузка мастики из работающего смесителя в бетоносмеситель в течение 15-30 с.
Общее время приготовления мастики должно быть не более 100 с, а с учетом выгрузки — не более 2 мин.
б. Технологические операции по приготовлению полимербетонной смеси КФ-Ж должны выполняться в соответствии с требованиями п.4.12, б настоящей Инструкции.
4.15. Перемешивание составляющих полимербетонной смеси ФАЭД.
а. Приготовление мастики следует проводить в следующем порядке:
подача в высокоскоростной смеситель отдозированного количества смолы ФАЭД и перемешивание в течение 10 с;
скорость вращения рабочего органа смесителя 600-800 об/мин;
подача в работающий смеситель отдозированного количества наполнителя и перемешивание смеси в течение 30-60 с;
подача в работающий смеситель отдозированного количества отвердителя ПЭПА и перемешивание смеси в течение 30-60 с;
выгрузка мастики из работающего смесителя в бетоносмеситель в течение 15-30 с.
Общее время приготовления мастики должно быть не более 2,0 мин, а с учетом выгрузки — не более 2,5 мин.
б. Технологические операции по приготовлению полимербетонной смеси ФАЭД должны выполняться в соответствии с п.4.12б настоящей Инструкции.
4.16. Перемешивание составляющих полимербетонной смеси ММА.
а. Перемешивание составляющих полимербетонной смеси ММА должно включать три стадии:
приготовление жидкого компаунда;
приготовление мастики;
приготовление полимербетонной смеси.
б. Приготовление жидкого компаунда следует проводить в следующем порядке:
измельчение больших кусков нефтяного парафина на частицы с размером не более 1 мм;
подача в смеситель мономера ММА и требуемых количеств измельченного нефтяного парафина и диметиланилина ДМА и перемешивание в течение 1-2 мин, скорость вращения рабочего органа смесителя 200-400 об/мин;
выгрузка приготовленного жидкого компаунда в накопительную емкость;
выдерживание жидкого компаунда в накопительной емкости в течение трех суток для полного растворения парафина.
в. Приготовление мастики следует проводить в следующем порядке:
подача в высокоскоростной смеситель отдозированных количеств жидкого компаунда и эмульсионного полистирола (стабилизатора) и перемешивание в течение 10-20 с; скорость вращения рабочего органа смесителя 600-800 об/мин;
подача в работающий смеситель отдозированного количества перекиси бензоила и перемешивание в течение 30 с;
подача в работающий смеситель отдозированного количества наполнителя и перемешивание смеси в течение 30-60 с;
выгрузка мастики из работающего смесителя в бетоносмеситель в течение 15-30 с.
Общее время приготовления мастики должно быть не более 2 мин, а с учетом выгрузки — не более 2,5 мин.
г. Технологические операции по приготовлению полимербетонной смеси ММА должны выполняться в соответствии с п.4.12б настоящей Инструкции.
4.17. Приготовление полимербетонных смесей должно осуществляться в бетоносмесителях принудительного действия.
4.18. Технологический процесс приготовления полимербетонной смеси должен проводиться при температуре окружающего воздуха не менее 15 град.С.
4.19. По окончании каждой смены бетоносмеситель следует тщательно очищать от остатков полимербетонной смеси путем загрузки в него щебня и перемешивания в течение 3 мин, после чего щебень выгружается из бетосмесителя.
5. ИЗГОТОВЛЕНИЕ ПОЛИМЕРБЕТОННЫХ ИЗДЕЛИЙ
Формование изделий из полимербетона
5.1. Технологический процесс формования полимербетонных изделий состоит из следующих операций:
чистка и смазка форм;
установка арматурных каркасов;
укладка полимербетонной смеси;
формование изделий.
5.2. Полимербетонные изделия должны изготавливаться в стальных формах, удовлетворяющих требования ГОСТ 18886-73*.
Допускается изготовление изделий в формах из двух материалов, обеспечивающих соблюдение требований ГОСТ 13015-75 или технических условий к качеству и точности изготовления изделий.
5.3. Сварные арматурные изделия и стальные закладные детали должны удовлетворять требованиям ГОСТ 10922-75, сварные товарные сетки — требованиям ГОСТ 8478-66, а монтажные петли — требованиям ГОСТ 5781-75.
5.4. Подготовка форм должна заключаться в очистке рабочих поверхностей от остатков полимербетона и смазки их следующим составом (части по массе):
эмульсол ЭТ (А) ………………………….. 55-60
графитовый порошок ……………………….. 35-40
вода ……………………………………. 5-10
Допускается смазка форм раствором битума в бензине, силиконовыми смазками или раствором низкомолекулярного полиэтилена в толуоле.
5.5. Время между окончанием приготовления полимербетонной смеси и формованием изделий должно составлять не более 10 мин.
5.6. Для укладки, разравнивания и заглаживания смеси в форме следует применять бетоноукладчики по ГОСТ 13531-74*.
Допускается производить укладку полимербетонной смеси в формы непосредственно из бетоносмесителя.
5.7. Уплотнение полимербетонной смеси в форме должно производиться на вибрационных площадках, отвечающих требованиям ГОСТ 17674-72 с обязательным наличием вертикальной составляющей колебаний. Амплитуда колебаний зависит от концентрации связующего и уточняется на пробных формовках. Допускается уплотнение смеси навесными вибраторами.
5.8. Продолжительность вибрирования должна быть 100+/-30 с. Признаком достаточного уплотнения полимербетонной смеси для тяжелых бетонов служит выделение на поверхности изделия связующего и прекращение интенсивного образования пузырьков воздуха.
Контроль качества уплотнения полимербетонной смеси для легких полимербетонов следует осуществлять в соответствии с ГОСТ 11051-70.
5.9. При уплотнении изделий из полимербетонов на пористых заполнителях следует выполнять виброформование с пригрузом, обеспечивающим давление 0,005 МПа.
Для предотвращения налипания полимербетонной смеси на поверхность пригруза необходимо между поверхностью пригруза и смесью предусмотреть прокладку однократного действия из полиэтиленовой пленки или металлическую крышку многократного использования, снимающуюся после завершения термообработки.
Отверждение полимербетонных изделий
5.10. Твердение отформованных изделий должно происходить при температуре не менее 15 град.С и нормальной влажности окружающего воздуха в течение 28 сут, для изделий из полимербетонов ММА — в течение 3+/-1 сут.
5.11. Для ускорения процесса твердения изделия из полимербетонов должны подвергаться термообработке, которую следует производить в камерах сухого прогрева. Сухой прогрев должен осуществляться электронагревателями, паровыми регистрами.
5.12. Длительность выдержки в формах полимербетонных изделий до распалубки и последующей термообработки должна быть при температуре окружающей среды:
17+/-2 град.С ………………………….. 12 ч
22+/-2 град.С …………………………… 8 ч
более 25 град.С ………………………… 4 ч
5.13. Распалубленные полимербетонные изделия должны подвергаться термообработке по следующим режимам:
для полимербетонов ФАМ (ФА), ПН, КФ-Ж: подъем температуры до 80±2 град.С — 2 ч, выдержка при температуре 80±2 град.С — 16 ч, спуск температуры до 20 град.С — 4 ч;
для полимербетонов ФАЭД: подъем температуры до 120±5 град.С 3 ч, выдержка при температуре 120±5 град.С — 14 ч, спуск температуры до 20 град.С — 6 ч.
5.14. Термообработку полимербетонных изделий объемом не менее 0,2 куб.м допускается производить непосредственно в формах по следующим режимам:
для полимербетонов ФАМ (ФА), ПН, КФ-Ж: выдержка при 20 град.С 1,5 ч, подъем температуры до 80±2 град.С — 1 ч, выдержка при температуре 80±2 град.С — 16 ч, спуск температуры до 20 град.С — 4 ч;
для полимербетонов ФАЭД: выдержка при 20 град.С — 1,5 ч, подъем температуры до 120±5 град.С — 2 ч, выдержка при температуре 120±5 град.С — 14 ч, спуск температуры до 20 град.С — 6 ч.
5.15. Изделия из полимербетона ММА запрещается подвергать термообработке.
6. КОНТРОЛЬ КАЧЕСТВА РАБОТ
6.1. Технический контроль качества работ по приготовлению полимербетонов и изготовлению изделий из них включает:
испытание исходных материалов (связующих, отвердителей, ускорителей твердения, пластификаторов, наполнителей, заполнителей) с целью установления их пригодности для приготовления полимербетонов;
контроль выполнения установленной технологии приготовления полимербетонных смесей (правильность хранения материалов, их дозирование, порядок и время перемешивания составляющих, укладку и уплотнение полимербетонной смеси);
соблюдение принятого режима твердения полимербетона;
проверку основных свойств (прочности на сжатие, объемной массы);
проверку требований к точности изготовления изделий.
6.2. Схема производства технического контроля качества работ по приготовлению полимербетонов и изготовлению изделий из них, а также периодичность контроля следует принимать в соответствии с прил.2 настоящей Инструкции.
6.3. Пробы полимербетонной смеси для контроля прочности полимербетона должны отбираться в соответствии с требованиями ГОСТ 18105-72*.
6.4. Определение прочности полимербетона следует производить по ГОСТ 10180-78.
6.5. Величины предельных отклонений полимербетонных изделий и конструкций от их номинальных размеров должны быть не выше приведенных в ГОСТ 13015-75.
7. ТЕХНИКА БЕЗОПАСНОСТИ
7.1. При производстве работ по изготовлению полимербетонных изделий необходимо соблюдать правила, предусмотренные главой СНиП по технике безопасности в строительстве; Санитарные правила организации технологических процессов, утвержденные Главным санитарно-эпидемиологическим управлением Минздрава СССР; требования настоящей Инструкции.
7.2. Работы следует производить при включенной приточно-вытяжной вентиляции. При внезапной остановке вентиляции работы прекратить и покинуть помещение, оставив двери открытыми.
7.3. В камерах тепловой обработки после загрузки в них полимербетонных изделий вытяжная вентиляция должна работать круглосуточно.
7.4. Необходимо систематически осуществлять контроль за состоянием воздушной среды в помещениях. Содержание вредных веществ в воздухе рабочей зоны не должно превышать предельно допустимых концентраций, указанных в Санитарных нормах проектирования промышленных предприятий.
7.5. Рабочие перед допуском к самостоятельной работе должны пройти курс обучения, инструктаж по технике безопасности и пожарной опасности.
7.6. Рабочие, занятые на изготовлении полимербетонных изделий, должны иметь спецодежду и индивидуальные защитные средства, состоящие из прорезиненного фартука, комбинезона из плотной ткани, резиновых сапог, резиновых перчаток, фильтрующего противогаза марки «А» (для аварийных ситуаций).
7.7. При поступлении на работу рабочие должны пройти предварительный медицинский осмотр. Периодические медицинские осмотры рабочих должны производиться не реже одного раза в 12 мес.
7.8. Для рабочих должны быть оборудованы гардеробные для хранения чистой одежды и белья и отдельно для спецодежды, умывальники и душ с горячей водой, а также медицинские аптечки.
7.9. Спецодежда рабочих должна быть застегнута, рукава плотно завязаны у запястий. Выполнение всех операций незащищенными руками не допускается. После окончания работы необходимо принимать горячий душ.
7.10. Рабочие должны пользоваться сокращенным рабочим днем и спецпитанием согласно списку производств, цехов и профессий с вредными условиями труда, утвержденному ВЦСПС.
Приложение 1
Основные термины и определения
+——————————————————————+
¦ Термины ¦ Определение ¦
+——————————————————————+
Полимербетон Представляет собой смесь термореактивных смол,
отвердителей и химически стойких наполнителей и
заполнителей различной крупности
Наполнитель Твердое (реже жидкое) вещество с размером частиц
менее 0,15 мм, вводимое в полимер
Вяжущее (связую- Представляет собой смолу с отвердителем, а при
щее) необходимости — с пластификаторами
Пластификатор Вещество, вводимое в полимеры с целью повышения
пластичности и эластичности полимербетона
Отвердитель Вещество, обуславливающее отверждение реакционно-
способных олигомеров (смол). По характеру
действия делятся на следующие группы:
собственно отвердители, молекулы которых, реаги-
руя с функциональными группами олигомера, входят
в структуру образующегося полимера;
инициаторы и катализаторы отверждения:
инициаторы вызывают отверждение олигомеров по
механизму радиальной полимеризации;
катализаторы ускоряют взаимодействие олигомеров
между собой или с отвердителем первой группы
Твердение (от- Процесс, при котором реакционноспособные
верждение) олигомеры необратимо превращаются в твердые
нерастворимые и неплавкие трехмерные полимеры
Полимербетон Полимербетон плотной структуры на синтетическом
тяжелый связующем и плотных химически стойких крупных и
мелких заполнителях, тяжелый (2200-2500 кг/куб.м)
по объемной массе
Полимербетон Полимербетон плотной структуры на синтетическом
легкий связующем, на пористом химически стойком крупном
заполнителе и химически стойком мелком
заполнителе плотном или пористом, легкий
(1500-1800 кг/куб.м) или облегченный (1800-2200
кг/куб.м) по объемной массе
ОСНОВНЫЕ БУКВЕННЫЕ ОБОЗНАЧЕНИЯ
Смолы
ФА — фурфурол-ацетоновая смола;
ФАМ — фурфурол-ацетоновая смола модифицированная;
ПН — ненасыщенная полиэфирная смола марки ПН-1 или ПН-63;
КФ-Ж — карбамидоформальдегидная смола;
ФАЭД — фурано-эпоксидная смола марки ФАЭД-20;
ММА — эфир метиловый метакриловой кислоты (мономер метилметакрилат).
Отвердители
БСК — бензолсульфокислота;
ГП — гидроперекись изопропилбензола;
СКА — солянокислый анилин;
ПЭПА — полиэтиленполиамин;
НК — нафтенат кобальта;
ПБ — перекись бензоила;
ДМА — диметиланилин.
Приложение 2
Схема пооперационного контроля качества приготовления
полимербетонной смеси и изготовления изделий
+—————————————————————————-+
¦ N ¦Контролирующие операции¦Периодичность¦Требования инструкции¦ГОСТ или ТУ¦
¦п.п.¦ ¦ контроля ¦ ¦ ¦
+—————————————————————————-+
А. Исходное сырье
1 Влажность наполнителя Каждую смену Взвешивание навески —
материала, не более 1%
по массе
2 Влажность мелкого за- То же Взвешивание навески —
полнителя (песка) материала, не более 0,5%
по массе
3 Влажность крупного за- » То же —
полнителя (щебня, гра-
вия)
4 Гранулометрический сос- Для каждой Требования пп.2.8-2.15 ГОСТ 9759-76,
тав заполнителя партии настоящей Инструкции ГОСТ 11991-76,
ГОСТ 8736-77,
ГОСТ 10268-70*
5 Удельная поверхность То же Не менее 2500 кв.см/г ГОСТ 3102-76
наполнителя
6 Кислотостойкость запол- » Не ниже 97% ГОСТ 473.1-72
нителей
7 Температура заполни- Два раза в Не более 30 град.С —
телей и наполнителей смену
перед дозировкой
Б. Приготовление полимербетонной смеси
8 Точность дозировочных Один раз в ФАМ, БСК+/-1% ГОСТ 13712-68**
устройств и правиль- месяц Наполнитель +/-1%
ность дозирования Заполнитель +/-2%
9 Температура расплав- Два раза в Не более 70 град.С —
ления БСК смену
10 Температура БСК перед Два раза в Не более 45 град.С —
дозированием смену
11 Время перемешивания То же Требования разд.4 нас- —
составляющих смеси тоящей Инструкции
В. Формование и отверждение полимербетонной смеси
12 Правильность сборки Каждое Внутренние размеры форм ГОСТ 18886-73*
форм изделие в пределах минусовых
допусков
13 Правильность установки То же Требования рабочих чер- ГОСТ 13015-75
арматурных каркасов и тежей
закладных деталей
14 Виброформование » Требования п.5.8 настоя- ГОСТ 17674-72,
щей Инструкции ГОСТ 11051-70
15 Продолжительность вы- Каждое Требования разд.5 нас- —
держки изделий до тер- изделие тоящей Инструкции
мообработки и в камерах
тепловой обработки
16 Контроль температуры в Автомати- По показателям термопар —
камерах тепловой обра- чески
ботки
Г. Готовая продукция
17 Размеры, дефекты по- Для каждого Требования п.6.5 настоя- ГОСТ 13015-75
верхности изделия щей Инструкции
18 Контроль и оценка од- Для каждой Испытание образцов-кубов ГОСТ 18105-72*,
нородности и прочнос- партии по- на сжатие не ниже проч- ГОСТ 10180-78
ти полимербетона лимербетона ности, указанной в рабо-
чих чертежах
Приложение 3
Усредненные физико-механические показатели
полимербетонов
+——————————————————————+
¦ ¦ ¦ Показатели полимербетонов ¦
¦ Физико-механические ¦ Единица +———————————¦
¦ свойства ¦измерения¦ тяжелых ¦ на пористых ¦
¦ ¦ ¦ ¦ заполнителях ¦
+——————————————————————+
Полимербетоны ФАМ (ФА)
Объемная масса кг/куб.м 2200-2400 1500-1900
Кратковременная прочность:
при сжатии кгс/кв.см 700-900 300-650
при растяжении кгс/кв.см 50-80 30-55
Модуль упругости при кгс/кв.см (200-320)10_3 (130-200)10_3
сжатии
Коэффициент Пуассона — 0,2-0,24 0,19-0,21
Удельная ударная вяз- Дж/кв.см 0,15-0,25 0,1-0,2
кость
Линейная усадка при % 0,1 0,1-0,15
отверждении
Водопоглощение за 24 ч % 0,05-0,3 0,1-0,4
Термостойкость по град.С 120-140 120-140
Мартенсу
Теплопроводность Вт/(мхК) 0,66-0,85 0,29-0,58
Морозостойкость, не циклов 300 300
ниже
Коэффициент термичес- 1/град.С (12-15)10_-6 (11-13)10_-6
кого расширения
Истираемость г/кв.см 0,018-0,21 0,025-0,35
Удельное электрическое
сопротивление:
поверхностное Ом 3,7х10_10 3,7х10_10
объемное ОмХсм 3,8х10_8 5,8х10_8
Тангенс угла диэлектри- — 0,05-0,06 0,02-0,05
ческих потерь при 50 Гц
и 65% относительной
влажности
Показатель горючести К — 0,14 0,14
Полимербетоны ФАЭД
Объемная масса кг/кв.см 2200-2400 1500-1800
Кратковременная прочность:
при сжатии кгс/кв.см 900-1100 500-850
при растяжении кгс/кв.см 90-110 30-90
Модуль упругости при кгс/кв.см (320-380)10_3 (120-180)10_3
сжатии
Коэффициент Пуассона — 0,26-0,28 0,24-0,26
Удельная ударная вяз- Дж/кв.см 0,35-0,45 0,2-0,3
кость
Линейная усадка при % 0,05-0,08 0,06-0,1
отверждении
Водопоглощение за 24 ч % 0,01 0,2-0,5
Термостойкость по град.С 120 120
Мартенсу
Теплопроводность Вт/(мхК) 0,66-0,85 0,29-0,58
Морозостойкость, не циклов 500 300
ниже
Коэффициент термичес- 1/град.С (10-14)10_-6 (10-14)10_-6
кого расширения
Истираемость г/кв.см 0,005-0,01 0,01-0,02
Тангенс угла диэлектри- — 0,04-0,05 0,03-0,05
ческих потерь при 50 Гц
и 65% относительной
влажности
Показатель горючести К 1 1
Полимербетоны ПН
Объемная масса кг/куб.см 2200-2400 1500-1800
Кратковременная прочность:
при сжатии кгс/кв.см 800-1000 500-850
при растяжении — 70-90 20-80
Модуль упругости при кгс/кв.см (280-360)10_3 (120-180)10_3
сжатии
Коэффициент Пуассона — — 0,2-0,22
Удельная ударная вяз- Дж/кв.см 0,2-0,25 0,1-0,2
кость
Линейная усадка при % 0,02-0,25 0,2-0,25
отверждении
Водопоглощение за 24 ч % 0,05-0,1 0,05-0,3
Термостойкость по град.С 80 80
Мартенсу
Теплопроводность Вт/(мхК) 0,62-0,8 0,29-0,58
Морозостойкость не циклов 300 300
ниже
Коэффициент термичес- 1/град.С (14-20)10_-6 (14-18)10_-6
кого расширения
Истираемость г/кв.см 0,015-0,025 0,02-0,03
Тангенс угла диэлектри- — 0,03-0,06 0,01-0,04
ческих потерь при 50 Гц
и 65% относительной
влажности
Показатель горючести К:
на смоле ПН-1 2,1 2,1
на смоле ПН-63 0,47 0,47
Полимербетоны КФ-Ж
Объемная масса кг/куб.м 2200-2400 1500-1800
Кратковременная прочность:
при сжатии кгс/кв.см 500-600 300-400
при растяжении — 30-40 25-40
Модуль упругости при кгс/кв.см (100-140)10_3 (90-100)10_3
сжатии
Коэффициент Пуассона — 0,22-0,24 0,2-0,21
Удельная ударная вяз- Дж/кв.см 0,15-0,25 0,1-0,2
кость
Линейная усадка при % 0,2-0,22 0,16-0,2
отверждении
Водопоглощение за 24 ч % 0,1-0,3 0,2-0,6
Теплостойкость по град.С 100-120 100-120
Мартенсу
Теплопроводность Вт/(мхК) 0,66-0,85 0,44-0,58
Морозостойкость, не циклов 200 200
ниже
Коэффициент термичес- 1/град.С (15-16)10_-6 (13-15)10_-6
кого расширения
Истираемость г/кв.см 0,02-0,03 —
Тангенс угла диэлектри- — 0,08-0,1 0,06-0,1
ческих потерь при 50 Гц
и 65% относительной
влажности
Показатель горючести К — 0,2 0,2
Полимербетоны ММА
Объемная масса кг/кв.см 2200-2400 1500-1800
Кратковременная прочность:
при сжатии кгс/кв.см 700-900 400-650
при растяжении кгс/кв.см 100-130 50-80
Модуль упругости при кгс/кв.см (100-150)10_3 (80-100)10_3
сжатии
Коэффициент Пуассона — 0,26-0,28 0,26-0,27
Линейная усадка при % 0,15-0,20 0,2-0,25
отверждении
Водопоглощение за 24 ч % 0,01 0,05-0,2
Термостойкость по град.С 60 60
Мартенсу
Теплопроводность Вт/(мхК) 0,66-0,85 0,29-0,58
Морозостойкость, не циклов 500 300
ниже
Коэффициент термичес- 1/град.С (12-16)10_-6 (12-18)10_-6
кого расширения
Тангенс угла диэлектри- — 0,04-0,05 0,02-0,04
ческих потерь при 50 Гц
и 65% относительной
влажности
Показатель горючести К — 2,1 2,1
1. ОСНОВНЫЕ ПОЛОЖЕНИЯ
2. МАТЕРИАЛЫ ДЛЯ ПРИГОТОВЛЕНИЯ ПОЛИМЕРБЕТОНОВ
Смолы, отвердители и пластификаторы
Требования к заполнителям
Требования к наполнителям
3. Составы полимербетонов
4. Приготовление полимербетонов
5. ИЗГОТОВЛЕНИЕ ПОЛИМЕРБЕТОННЫХ ИЗДЕЛИЙ
Формование изделий из полимербетона
Отверждение полимербетонных изделий
6. КОНТРОЛЬ КАЧЕСТВА РАБОТ
7. ТЕХНИКА БЕЗОПАСНОСТИ
Приложение 1. Основные термины и определения
ОСНОВНЫЕ БУКВЕННЫЕ ОБОЗНАЧЕНИЯ
Смолы
Отвердители
Приложение 2. Схема пооперационного контроля качества приготовления полимербетонной смеси и изготовления изделий
Приложение 3. Усредненные физико-механические показатели полимербетонов